Call: Eurostars CoD14 of the Horizon Europe Framework Program H2020, financed by CDTI in the international inter-company call
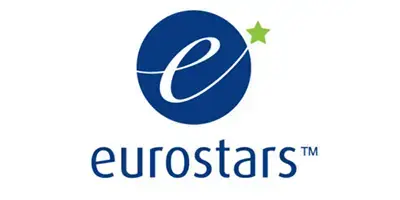

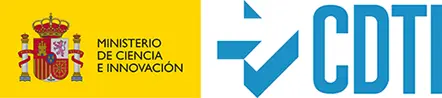
SUMMARY
The use of precision temporary masks is a very common operation in metallic finishing treatments. It consists of protecting specific areas of the surface that should not be treated, an operation known as “masking”. The use of masks can represent 80% of the total cost of operations in the treatment of parts with complex geometry that must receive different surface treatments in each of their areas. The high cost of this stage is due to the mask removal process, which takes a long time and generates fluctuating and narrow margins.
Almost all surface treatment companies use masks in their process. Specifically, those that work for the aeronautical sector can use them in 60% of the total treated parts. For this reason, the metal finishing industry is looking for a profitable solution that minimizes time and costs derived from the masking process.
THERMOMASK’s general objective is to develop and validate in a real environment a thermo-strippable mask that is easy to apply and remove, suitable for use in aggressive environments. Likewise, the project proposes the development of new equipment that will facilitate the removal of the mask by means of infrared heating of the specific area to be removed. The project focuses mainly on the application of the mask and the use of the peeling equipment by surface treatment companies that require selective coatings, mainly for the aerospace and/or automotive industry, where their elements have a high added value.
The consortium is made up by 3 SMEs, two of them of Spanish origin (GAITEK and ELHCO) and one of French origin (RESCOLL).
The use of precision temporary masks is a very common operation in metallic finishing treatments. It consists of protecting specific areas of the surface that should not be treated, an operation known as “masking”. The use of masks can represent 80% of the total cost of operations in the treatment of parts with complex geometry that must receive different surface treatments in each of their areas. The high cost of this stage is due to the mask removal process, which takes a long time and generates fluctuating and narrow margins.
Almost all surface treatment companies use masks in their process. Specifically, those that work for the aeronautical sector can use them in 60% of the total treated parts. For this reason, the metal finishing industry is looking for a profitable solution that minimizes time and costs derived from the masking process.
THERMOMASK’s general objective is to develop and validate in a real environment a thermo-strippable mask that is easy to apply and remove, suitable for use in aggressive environments. Likewise, the project proposes the development of new equipment that will facilitate the removal of the mask by means of infrared heating of the specific area to be removed. The project focuses mainly on the application of the mask and the use of the peeling equipment by surface treatment companies that require selective coatings, mainly for the aerospace and/or automotive industry, where their elements have a high added value.
The consortium is made up by 3 SMEs, two of them of Spanish origin (GAITEK and ELHCO) and one of French origin (RESCOLL).
OBJECTIVES OF THE PROJECT
The THERMOMASK project proposes a 40% cost reduction in masking operations through two action strategies. Firstly, the reduction of the required thickness of the mask to the minimum for its easy peeling. Secondly, the simplification in the peeling and cleaning process, thanks to the adhesion loss that the mask suffers in the presence of heat.
The achievement of these objectives requires obtaining the following results in the project:
ELHCO’s specific technical objectives of the project are the following:
OTHER PROJECTS
BOOSTing 3D printed METALs through specific surface treatment methods and advanced tools
Estado actual: In progressDefinitive replacement of hexavalent hard chrome in the aeronautical sector
Actual state: In progressInvestigation and modelling of Hydrogen effusion in electrochemically plated ultra-high-strength-steels used for landing gear structures
Actual state: FinalizedDevelopment of a viable and sustainable alternative to hexavalent hard chrome for functional applications in aeronautical and automotive industries.
Actual state: Finalized