Call: This project has received funding from the Eurostars-3 CoD5 program with co-financing from CDTI and the Horizon Europe Framework Programme of the European Union for Research and Innovation
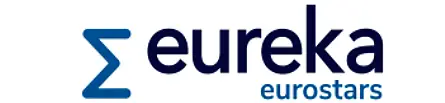
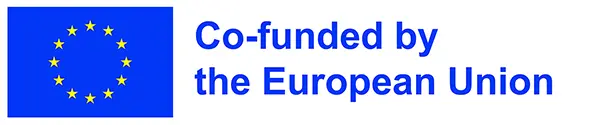
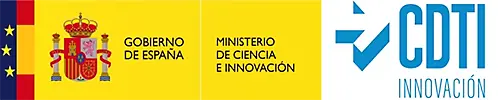
SUMMARY
Metal Additive manufacturing (MAM) is replacing current production methods, as it enables the manufacturing of parts with complex geometries for various industries, offering potential benefits in terms of weight, functionality, production time, and manufacturability. However, post-processing is essential, limiting further penetration into the MAM market due to:
• Particular microstructure of MAM parts
• Non-uniformity in geometry.
• Hard-to-reach, such as recesses and holes.
This results in a post-processing cost increase of approximately 20% and the difficulty of ensuring compliance with final requirements in terms of corrosion protection. If appropriate surface treatments are not developed, the expected advancement of this technology may not occur, especially for certain materials like aluminum.
There are different technologies for MAM, but among them, Powder Bed Fusion (PBF) has the advantage of allowing the fabrication of parts with high structural complexity and a high level of precision. Among the numerous metals and alloys that can be processed using PBF technology, aluminum alloys are of great interest to the automotive and aerospace industries due to their high strength and stiffness-to-weight ratio, good wear and corrosion resistance, and their potential for recycling.
Therefore, research and innovation are necessary to create specific protection measures, either by changing the printing conditions of MAM, adjusting post-treatments, and/or developing customized surface treatments. Additionally, design guidelines oriented towards post-processing and surface analysis methods are needed. To achieve this goal, new component design strategies, production protocols, and products are required, along with better control and understanding of defects introduced by manufacturing conditions. Therefore, the main objective of BOOST3DMETAL is the development of advanced tools and specific products for the manufacturing and post-processing of aluminum MAM components, covering from the design of the part to the final product.
Metal Additive manufacturing (MAM) is replacing current production methods, as it enables the manufacturing of parts with complex geometries for various industries, offering potential benefits in terms of weight, functionality, production time, and manufacturability. However, post-processing is essential, limiting further penetration into the MAM market due to:
• Particular microstructure of MAM parts
• Non-uniformity in geometry.
• Hard-to-reach, such as recesses and holes.
This results in a post-processing cost increase of approximately 20% and the difficulty of ensuring compliance with final requirements in terms of corrosion protection. If appropriate surface treatments are not developed, the expected advancement of this technology may not occur, especially for certain materials like aluminum.
There are different technologies for MAM, but among them, Powder Bed Fusion (PBF) has the advantage of allowing the fabrication of parts with high structural complexity and a high level of precision. Among the numerous metals and alloys that can be processed using PBF technology, aluminum alloys are of great interest to the automotive and aerospace industries due to their high strength and stiffness-to-weight ratio, good wear and corrosion resistance, and their potential for recycling.
Therefore, research and innovation are necessary to create specific protection measures, either by changing the printing conditions of MAM, adjusting post-treatments, and/or developing customized surface treatments. Additionally, design guidelines oriented towards post-processing and surface analysis methods are needed. To achieve this goal, new component design strategies, production protocols, and products are required, along with better control and understanding of defects introduced by manufacturing conditions. Therefore, the main objective of BOOST3DMETAL is the development of advanced tools and specific products for the manufacturing and post-processing of aluminum MAM components, covering from the design of the part to the final product.
Objectives of the project:
The main objective of the BOOST3DMETAL project is to promote aluminum additive manufacturing and, specifically, Powder Bed Fusion (PBF) technology, through the development and validation of:
The specific objectives of the project are:
- 1Produce high-value-added and properly post-processed aluminum parts at a competitive price that allows the entry of the product into the market.
- 2Launch new chemical products for surface treatments of aluminum parts manufactured through metal additive manufacturing (MAM). Ensure that all products used are safe and comply with the REACH regulation.
- 3Include new surface treatment services for aluminum parts manufactured through MAM.
- 4Develop image-based surface analysis software to control roughness, morphology, and coverage power even in holes and recesses using a borescope.
- 5Implement a surface analysis service using the software developed during the project.
- 6Create a predictive assistant (software) containing guidelines oriented towards post-processing for the design of parts and surface treatments.
- 7Offer consulting and training services, based on post-processing-oriented guidelines for the design of parts and surface treatments.
For all the specific objectives mentioned above, the expected type of development is incremental, as innovation is based on existing technology and an established business model (common markets and channels).
OTHER PROJECTS
Definitive replacement of hexavalent hard chrome in the aeronautical sector
Actual state: In progressDevelopment of new masks based on thermo-strippable resins for selective surface treatments.
Actual state: FinalizedInvestigation and modelling of Hydrogen effusion in electrochemically plated ultra-high-strength-steels used for landing gear structures
Actual state: FinalizedDevelopment of a viable and sustainable alternative to hexavalent hard chrome for functional applications in aeronautical and automotive industries.
Actual state: Finalized