Call: Clean-Sky 2 of the Horizon Europe Framework Programme H2020
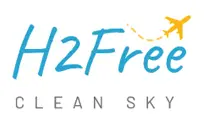
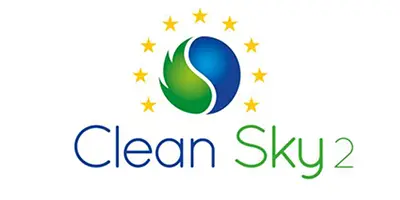
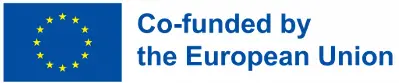
SUMMARY
One drawback associated to Ultra High Strength Steels (UHSS) coated components is the risk of hydrogen embrittlement (HE) and delayed hydrogen fracture of the part. This problem has been tackled by developing LHE (Low HE) processes and by applying a degassing stage. The standard degassing process is applied equally to the components regardless UHSS or coating composition/morphology. However, it is known that the nature and structure of both the base material and the coating have a great influence in the hydrogen intake and degassing efficiency. Thus, there is much room for improvement if a better understanding of the underlying phenomena of electrochemically deposited corrosion protection layers of UHSS parts on hydrogen degassing is achieved.
As there are no experimental techniques to measure hydrogen content or HE in a specific part of a real component at an industrial environment, modelling and simulation approaches, developed with a strong experimental base, are expected to provide the keys to process improvement.
As such, if a verified model correlating the influence of undesirable layer structures of electrochemically deposited protection layers of UHSS parts on hydrogen degassing was created, the remaining hydrogen concentration in steel parts and the probability for hydrogen embrittlement would be predicted. The industrial objective is to minimize rework and scrap of ultra-high-strength-steel parts and the related environmental impacts.
With its digital approach, H2Free will accelerate materials modelling uptake into European industrial decision making and link all partners to central European materials modelling platforms and activities.
The project brings together a strong consortium composed of 4 outstanding research centres and 2 SMEs with complementary profiles and large expertise in their respective fields, covering the capabilities necessary to carry it out.
One drawback associated to Ultra High Strength Steels (UHSS) coated components is the risk of hydrogen embrittlement (HE) and delayed hydrogen fracture of the part. This problem has been tackled by developing LHE (Low HE) processes and by applying a degassing stage. The standard degassing process is applied equally to the components regardless UHSS or coating composition/morphology. However, it is known that the nature and structure of both the base material and the coating have a great influence in the hydrogen intake and degassing efficiency. Thus, there is much room for improvement if a better understanding of the underlying phenomena of electrochemically deposited corrosion protection layers of UHSS parts on hydrogen degassing is achieved.
As there are no experimental techniques to measure hydrogen content or HE in a specific part of a real component at an industrial environment, modelling and simulation approaches, developed with a strong experimental base, are expected to provide the keys to process improvement.
As such, if a verified model correlating the influence of undesirable layer structures of electrochemically deposited protection layers of UHSS parts on hydrogen degassing was created, the remaining hydrogen concentration in steel parts and the probability for hydrogen embrittlement would be predicted. The industrial objective is to minimize rework and scrap of ultra-high-strength-steel parts and the related environmental impacts.
With its digital approach, H2Free will accelerate materials modelling uptake into European industrial decision making and link all partners to central European materials modelling platforms and activities.
The project brings together a strong consortium composed of 4 outstanding research centres and 2 SMEs with complementary profiles and large expertise in their respective fields, covering the capabilities necessary to carry it out.
OBJECTIVES OF THE PROJECT
The main objective of the H2Free project is to develop a practical guideline for hydrogen degassing of UHS-steels plated with LHE-Zn-Ni, with the aim of saving production costs and allowing Zn-Ni to overtake Cd coatings. The guideline will contain simple rules/formulas to provide criteria to design the degassing process, based on experimental data and on modelling to predict the hydrogen effusion in coated UHSS, the remaining hydrogen concentration in the components and so the probability of hydrogen embrittlement.
For this purpose, the following listed specific objectives will be pursued:
OTHER PROJECTS
BOOSTing 3D printed METALs through specific surface treatment methods and advanced tools
Estado actual: In progressDefinitive replacement of hexavalent hard chrome in the aeronautical sector
Actual state: In progressDevelopment of new masks based on thermo-strippable resins for selective surface treatments.
Actual state: FinalizedDevelopment of a viable and sustainable alternative to hexavalent hard chrome for functional applications in aeronautical and automotive industries.
Actual state: Finalized